// Check if the article Layout ?>
Fugenlose Hülle
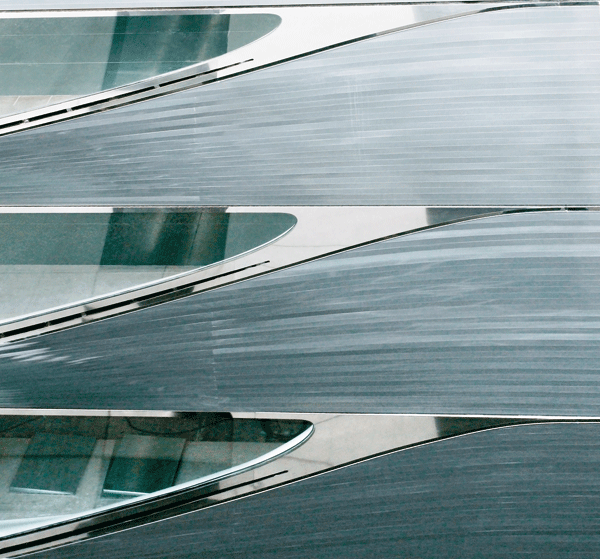
Zur Fertigung von Freiformfassaden mit innovativen Bausystemen
von Michael Purzer, Frener & Reifer
Für die freigeformte, fugenlos erscheinende Aluminiumhülle eines Bürogebäudes in London adaptierten Planer und Fassadenbauer ein aus dem Schiffsbau kommendes Bausystem. Maßgebend waren unter anderem die Kriterien der kostengünstigen und rationellen Fertigung und Montage.
Der Ansatz wurde nun auf die Erfordernisse des Bauwesens in einen qualitätsgesicherten Fertigungs-, Logistik- und Montagekontext eingebettet. Dies erforderte die Entwicklung einer weitestgehend standardisierten Unterkonstruktion mit entsprechenden Verbindungselementen zur Montage der Einzelbauteile untereinander und für die Koppelung an die bauseitige Primärkonstruktion. Die zum Teil teflonbeschichteten Verbindungselemente mussten kostengünstig und rationell zu montieren sein und ein Gleiten bzw. eine Rotation relativ zur Unterkonstruktion zulassen. Die Verbindungselemente und die gewählte Geometrie der Unterkonstruktion ermöglichten große, fast fugenlos wirkende Flächen.
Das NC-gefertigte Unterkonstruktionssystem definiert die Geometrie der Gebäudeoberfläche. Die Spantrahmen werden in Schnittebenen angeordnet, die annähernd orthogonal zum jeweiligen Bereich der Gebäudekontur ausgerichtet sind.
Das NC-gefertigte Unterkonstruktionssystem definiert die Geometrie der Gebäudeoberfläche. Die Spantrahmen werden in Schnittebenen angeordnet, die annähernd orthogonal zum jeweiligen Bereich der Gebäudekontur ausgerichtet sind.
Seit der Übertragung der nicht-uniformen rationalen B-Splines, kurz NURBS-Flächen, in den Software-Bereich und der damit verbundenen schöpferischen Freiheit sind bei Alltagsgegenständen Freiformflächen allgegenwärtig. In der Architektur ist eine starke Tendenz zu frei gestalteten Gebäudehüllen erkennbar. Allerdings scheint die Fertigung in alle Richtungen gekrümmter großformatiger Bauteile aufgrund der kleinen Serie und der hohen Kosten fast unmöglich: Beinahe jedes einzelne Bauteil wird zum Prototyp.
Da Freiformflächen meist nicht abwickelbar sind und eine teure rein handwerkliche dreidimensionale Verformung einzelner Komponenten nötig wäre, ist die Triangulierung der Oberfläche naheliegend. Sie erfordert jedoch einen hohen Planungsaufwand.
Auch das Roll-Schweiß-Verfahren verbunden mit neu entwickelten Fassadenunterkonstruktionen und entsprechender Softwareunterstützung ist eine Methode, frei geformte Fassadenteile auf Grundlage des klassischen Spenglerhandwerks vorzukonfektionieren. Die industrielle Weiterentwicklung der Stegfalzdeckung führte zu einem durch einen numerisch gesteuerten Rollformprozess hergestellten Stegfalzprofil. Mit seinem variablen Flächenumriss lassen sich beinahe alle gekrümmten Flächen beschreiben - zum Nachteil der architektonischen Eleganz aufgrund der starken Strukturierung der Stöße.
Freiformoberflächen mit geringer Krümmung lassen sich durch die geeignete Wahl der Unterkonstruktion elastisch in Form bringen. Für die Fassade des Bürogebäudes in London von Amanda Levete Architects wurde ein aus dem Schiffsbau hergeleiteter Ansatz gewählt: Die Bauweise erlaubt die Konstruktion von fast beliebig gekrümmten Freiformflächen durch den Einsatz spezieller Aluminium-Strangpressprofile, die die Funktion der Planken übernehmen. Nach der Plankenmontage auf die Spantenkonstruktion wird die Fläche durch Verschweißen der Säume geschlossen und die Profilfugen mit Epoxidharz-Kitt versiegelt. Erst nach dem kompletten Zusammenbau wird der Schiffsrumpf mittels Primer und Nasslack beschichtet, sodass sich die Stoßstrukturierung beinahe auflöst.
Da Freiformflächen meist nicht abwickelbar sind und eine teure rein handwerkliche dreidimensionale Verformung einzelner Komponenten nötig wäre, ist die Triangulierung der Oberfläche naheliegend. Sie erfordert jedoch einen hohen Planungsaufwand.
Auch das Roll-Schweiß-Verfahren verbunden mit neu entwickelten Fassadenunterkonstruktionen und entsprechender Softwareunterstützung ist eine Methode, frei geformte Fassadenteile auf Grundlage des klassischen Spenglerhandwerks vorzukonfektionieren. Die industrielle Weiterentwicklung der Stegfalzdeckung führte zu einem durch einen numerisch gesteuerten Rollformprozess hergestellten Stegfalzprofil. Mit seinem variablen Flächenumriss lassen sich beinahe alle gekrümmten Flächen beschreiben - zum Nachteil der architektonischen Eleganz aufgrund der starken Strukturierung der Stöße.
Freiformoberflächen mit geringer Krümmung lassen sich durch die geeignete Wahl der Unterkonstruktion elastisch in Form bringen. Für die Fassade des Bürogebäudes in London von Amanda Levete Architects wurde ein aus dem Schiffsbau hergeleiteter Ansatz gewählt: Die Bauweise erlaubt die Konstruktion von fast beliebig gekrümmten Freiformflächen durch den Einsatz spezieller Aluminium-Strangpressprofile, die die Funktion der Planken übernehmen. Nach der Plankenmontage auf die Spantenkonstruktion wird die Fläche durch Verschweißen der Säume geschlossen und die Profilfugen mit Epoxidharz-Kitt versiegelt. Erst nach dem kompletten Zusammenbau wird der Schiffsrumpf mittels Primer und Nasslack beschichtet, sodass sich die Stoßstrukturierung beinahe auflöst.
Ausgangspunkt der Metallbauplanung war das mit der Software »Rhino« erstellte Modell der Architekten, das ausschließlich die Gebäudehülle (Planken) definierte. Für die Abwicklung der komplexen Fassadengestalt war ein an ein parametrisches Geometriemodell angelehntes durchgängiges Planungskonzept nötig, das die Individualität der einzelnen Bauteilkomponenten berücksichtigt. Dieses Planungstool stellt die Beibehaltung der Einzelbauteil-Identität sicher, ausgehend von der Planung über die verschiedenen Produktionsprozesse bis zur Baustellenmontage. Das gesamte Projekt entstand in Zusammenarbeit mit dem IBK II - Prof. Stefan Behling der Universität Stuttgart.
Den ausführlichen Beitrag finden Sie in: DETAIL 5-2010, S. 464ff.
Fotos oben und unten: Gidon Fuehrer/Amanda Levete Architects; Foto Mitte: Frener & Reifer, Brixen