// Check if the article Layout ?>
Maximum load-carrying capacity with minimum material input
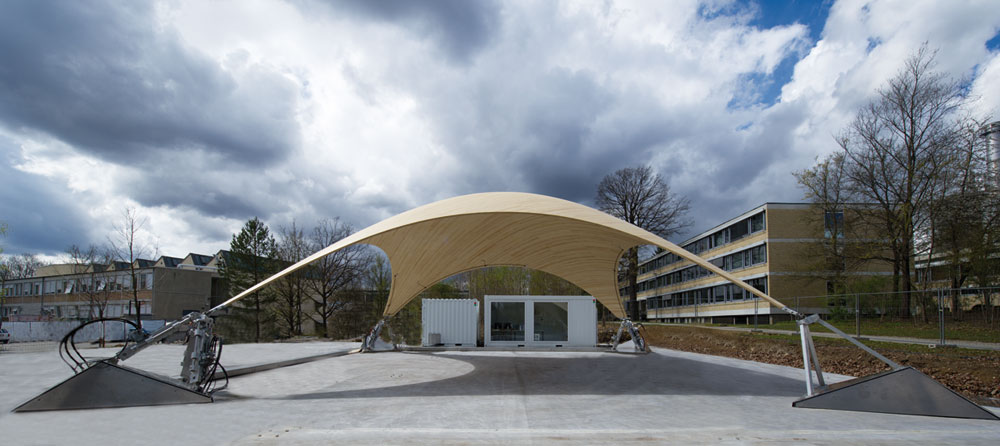
A hydraulic drive designed specifically for supporting structures, which can automatically compensate loads, has been developed by researchers at the University of Stuttgart in conjunction with Bosch Rexroth.
A wooden shell much thinner than considered possible before was constructed for the project. With a thickness of only four centimetres, the shell covers an area of over 100 m². The extreme slenderness of the shell is attributable to the fact that this is an adaptive structure. The prototype on the campus in Vaihingen was first presented on April 16th 2012 .
Buildings have generally always been planned for a certain maximum load. Such a maximum load however usually occurs very rarely and is limited to a short period of time. A large proportion of the building material used nowadays therefore serves to bear these extremely rare maximum loads, but is in fact hardly ever really made use of. The aim of the ultra-lightweight design developed at the University of Stuttgart is to achieve a drastic saving in material and an improved reaction to dynamic loads, through active manipulation of the structure.
In the case of the wooden shell in Stuttgart, this manipulation is achieved via hydraulic drives: these drives are positioned at the support points of the shell and produce movements, which specifically compensate deformations and material strains caused by wind, snow and other loads.
In the case of the wooden shell in Stuttgart, this manipulation is achieved via hydraulic drives: these drives are positioned at the support points of the shell and produce movements, which specifically compensate deformations and material strains caused by wind, snow and other loads.
In this project, Bosch Rexroth joined forces with ILEK (Institute for Lightweight Structures and Conceptual Design) and ISYS (Institute for System Dynamics) at the University of Stuttgart to be the first in realising a large-scale adaptive building. The wooden shell is mounted on four points. Three of the support points can be moved individually and positioned freely using hydraulic cylinders. Sensors register the load measurements at various points of the structure.
Specific support point movements counteract changing loads (such as through snow or wind) thereby reducing deformation and material tension. Much less material is therefore required for the shell construction compared to conventional, passive construction methods. The load balance is achieved using a Rexroth control system, which has been specially developed for hydraulic drives. The control system is mainly responsible for the complex hydraulic regulation of the shell structure. In this way, the structure is able to react to changes in the load within milliseconds.
Specific support point movements counteract changing loads (such as through snow or wind) thereby reducing deformation and material tension. Much less material is therefore required for the shell construction compared to conventional, passive construction methods. The load balance is achieved using a Rexroth control system, which has been specially developed for hydraulic drives. The control system is mainly responsible for the complex hydraulic regulation of the shell structure. In this way, the structure is able to react to changes in the load within milliseconds.
Active vibration damping and adaptation to changing loads is useful in many parts of the building industry, such as for stadium roofs, high-rise buildings, wide-spanning façade constructions or bridges. The results of the research project at the University of Stuttgart therefore allow a completely new style of construction: a style that remarkably increases the efficiency of supporting structures as well as being resource-friendly. The active damping of dynamic loads (for example due to effects of wind, earthquakes or explosions) permits a drastic weight reduction, as well as reducing material fatigue and structural damage.
In order to actively compensate loads and vibrations, it is first necessary to record or predict these influencing factors precisely. A second step involves calculation and realisation of the required counter-movements in real time. Researchers at the University of Stuttgart have developed simulation models which allow an exact prediction of the behaviour of the structure for this purpose. These take into account material stress as well as vibration behaviour under the influence of static and dynamic loads. The simulation models serve as a basis for development of control concepts, which calculate the required counter-movements for compensation of load and vibration effects according to the recorded measurements. These movements are then implemented precisely by the hydraulic system.
In order to actively compensate loads and vibrations, it is first necessary to record or predict these influencing factors precisely. A second step involves calculation and realisation of the required counter-movements in real time. Researchers at the University of Stuttgart have developed simulation models which allow an exact prediction of the behaviour of the structure for this purpose. These take into account material stress as well as vibration behaviour under the influence of static and dynamic loads. The simulation models serve as a basis for development of control concepts, which calculate the required counter-movements for compensation of load and vibration effects according to the recorded measurements. These movements are then implemented precisely by the hydraulic system.
ILEK and ISYS jointly developed the scientific basis of the project over the past years, while Bosch Rexroth supplied the active elements of the prototype. In close collaboration with the University of Stuttgart, the company managed the project work, selection and design of the hydraulic system and its initial operation.
ILEK is a pioneer in research in the field of adaptive systems in the building industry; a first, small-scale prototype was already constructed with the sponsor from Stuttgart some years ago. The core competence of ISYS includes the analysis and specific influence of dynamic systems. For this purpose, the institute develops regulatory structures that create coordinated movements of the supporting structure. Bosch Rexroth is one of the world’s leading specialists in the field of drive and control technologies.
The project is integrated as a functional model in the Research Unit 'Hybrid Intelligent Construction Elements' supported by the DGF (German Research Foundation). This Research Unit brings together experts in the fields of mechanical engineering, aerospace engineering, civil engineering and process engineering.
Project participants
ILEK is a pioneer in research in the field of adaptive systems in the building industry; a first, small-scale prototype was already constructed with the sponsor from Stuttgart some years ago. The core competence of ISYS includes the analysis and specific influence of dynamic systems. For this purpose, the institute develops regulatory structures that create coordinated movements of the supporting structure. Bosch Rexroth is one of the world’s leading specialists in the field of drive and control technologies.
The project is integrated as a functional model in the Research Unit 'Hybrid Intelligent Construction Elements' supported by the DGF (German Research Foundation). This Research Unit brings together experts in the fields of mechanical engineering, aerospace engineering, civil engineering and process engineering.
Project participants
- ILEK - Institute for Lightweight Structures and Conceptual Design, University of Stuttgart: Prof. Dr.-Ing. Dr.-Ing. E.h. Werner Sobek, M. Eng. Stefan Neuhäuser, Dipl.-Ing. Christoph Witte, Dr.-Ing. Walter Haase
- ISYS - Institute for System Dynamics, University of Stuttgart: Prof. Dr.-Ing. Oliver Sawodny, Dipl.-Ing. Martin Weickgenannt, Dr.-Ing. Eckhard Arnold
- IBK - Institute for Construction Materials and Building Construction at the University of Applied Sciences RheinMain Wiesbaden: Prof. Leander Bathon
- IfW - Institute for Machine Tools at University of Stuttgart: Prof. Uwe Heisel
- Bosch Rexroth AG, Lohr a. Main: Dr. Johannes Grobe, André Fella